- Boîtier industriel personnalisé
- Certification IP65/IP66
- Faible MOQ à partir de 1 PC
Votre fabricant professionnel de boîtiers PLC
Le boîtier PLC KDM convient à une gamme de systèmes de contrôle PLC tels que les PLC Allen Bradley, les PLC Mitsubishi, les PLC General Electric (GE), les PLC ABB, les PLC Siemens, les PLC Hitachi, etc. Nos boîtiers PLC sont disponibles dans différentes conceptions, configurations et configurations pour abriter les panneaux de contrôle PLC et SCADA. Chez KDM Steel, nous savons que les systèmes de contrôle industriels jouent un rôle majeur dans l'automatisation moderne et le processus de production efficace.
Avec plus de 10 ans d'expérience dans le secteur de la fabrication de boîtiers électriques, notre équipe technique choisit les meilleurs matériaux, tout en utilisant des équipements de coupe et des technologies de fabrication appropriés.
Série de boîtiers PLC KDM
Envoyez votre demande sur le boîtier PLC KDM
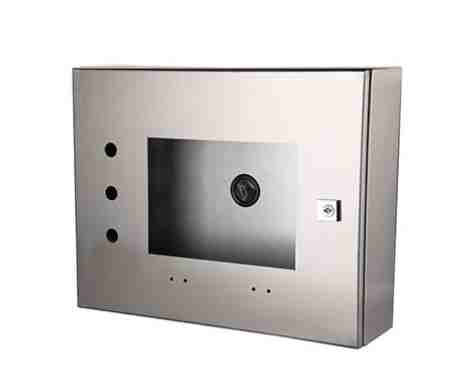
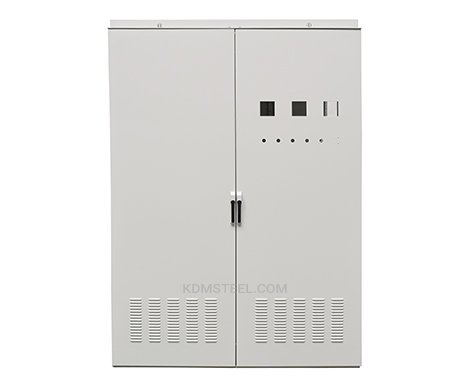
Que vous ayez besoin d'un boîtier PLC avec des options de verrouillage/verrouillage, des boutons-poussoirs faciles d'accès, un double accès, plusieurs portes ou des options de fenêtre, KDM Steel propose des boîtiers PLC de haute qualité et abordables.
Les ingénieurs de KDM Steel vous guideront tout au long de la conception assistée par ordinateur 2D et 3D ou des concepts de conception pour votre boîtier PLC. Parlez à nos ingénieurs dès aujourd'hui pour un boîtier PLC sur mesure.
- Capacité de production
- Guide d'achat
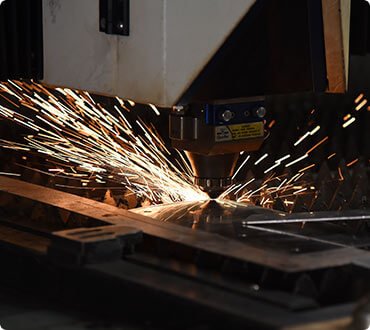
Machine de découpe laser haute performance 4000W, précision +/- 0,05mm. Pas de bavure, pas de rayures.
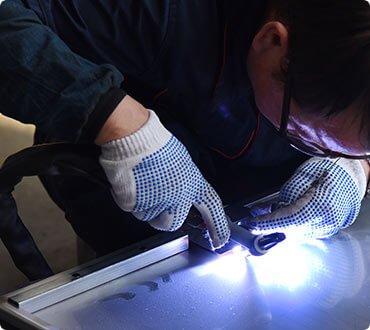
Équipement de soudage flexible multifonctionnel, haute précision, aucune déformation.
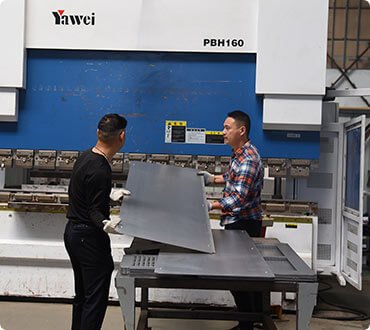
Précision de pliage de +/- 0,5 mm, surface lisse sans marques de pliage.
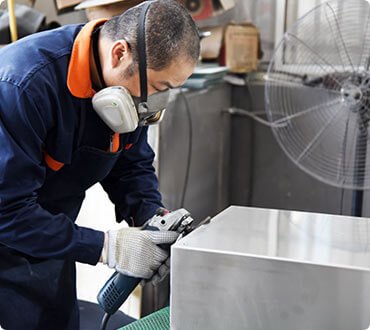
Plus de 10 ouvriers expérimentés en soudage, apparence générale parfaite.
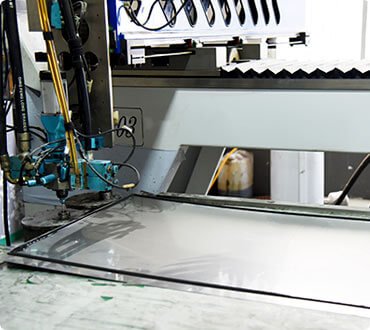
Machines de moussage à grande vitesse et précision, joint rapide et qualifié
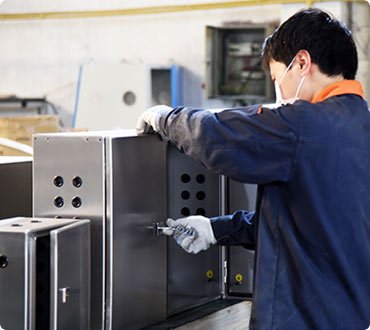
L'équipe d'assemblage experte, une qualité d'assemblage constante sur chaque boîtier KDM
KDM : votre fabricant professionnel de boîtiers PLC
Selon le type d'application, le boîtier PLC KDM se présente sous la forme d'un boîtier électrique intérieur ou d'un boîtier électrique extérieur.
Contrairement à la plupart des fabricants de boîtiers électriques du marché, les boîtiers PLC KDM sont conçus pour des environnements spécifiques.
Soudure de boîtiers d'automates programmables
Les options disponibles peuvent inclure un boîtier NEMA de type 1, 2, 3, 3R, 3S, 3X, 3RX, 3SX, 4, 4X, 5, 6, 6P, 7, 8, 9, 10, 11, 12, 12K ou 13.
De plus, le boîtier PLC KDM est livré sous la forme boîtier PLC autonome, boîtier PLC à montage mural, boîtier PLC modulaire, boîtier PLC résistant aux intempéries, Boîtier PLC avec fenêtre, boîtier PLC ventilé, entre autres modèles.
Le boîtier PLC KDM est facile à installer ou à accéder, peut avoir un bouton marche/arrêt rapide sur la porte, un petit écran pour la surveillance ou le contrôle des processus, des indicateurs LED sur le panneau et une conception facile de gestion des câbles ou des fils.
Accessoires pour boîtiers PLC
Le boîtier PLC KDM, également appelé armoire PLC ou boîtier de panneau PLC, est un accessoire conforme aux normes CE, RoHS, IEC et NEMA fabriqué en acier, en acier galvanisé ou en acier inoxydable (304.316L).
Il est spécifiquement conçu pour abriter tous les panneaux de contrôle industriels et les processeurs afin de garantir la sécurité et la protection.
Une raison pour laquelle le boîtier PLC KDM est spécialement conçu pour protéger tous les systèmes de contrôle sensibles.
Fabrication de boîtiers d'automates programmables
Envoyez votre demande maintenant
Boîtier PLC – Le guide complet des questions fréquemment posées
L’automatisation des processus de fabrication et industriels est le point clé de chaque installation réussie.
Pour rendre les processus aussi irréprochables que possible, des systèmes PLC ont été introduits.
Dans cet article, nous allons essayer d'expliquer comment fonctionnent ces systèmes et pourquoi ils ont besoin des boîtiers les plus robustes pour le faire.
- Qu'est-ce qu'un PLC ?
- Comment fonctionne le PLC ?
- Quels types de boîtiers PLC KDM peut-il proposer ?
- Pouvez-vous décrire le système électrique dans lequel le boîtier PLC est utilisé ?
- De quelles options de montage dispose-t-on avec les boîtiers PLC KDM ?
- Pouvez-vous nommer les matériaux utilisés pour fabriquer des boîtiers PLC ?
- Comment tester la sécurité des boîtiers PLC contre les effets environnementaux dangereux ?
- Qu'en est-il de la gestion du bruit et de la chaleur du boîtier PLC ?
- Dois-je vérifier les conditions du PLC avant de le démarrer ?
- Comment entretenir efficacement le boîtier et les composants internes d'un PLC ?
Qu'est-ce qu'un PLC ?
Un contrôleur logique programmable (PLC) est un système industriel ordinateur numérique qui a été créé et adapté pour le contrôle des processus de fabrication.
Les PLC ont été développés pour la première fois dans l'industrie automobile pour fournir des contrôleurs flexibles et facilement programmables pour remplacer les relais, les minuteries et les séquenceurs câblés.
Depuis lors, ils ont été largement adoptés comme contrôleurs d’automatisation de haute fiabilité adaptés aux environnements difficiles.
Les PLC peuvent aller de petits dispositifs modulaires avec une douzaine d'entrées et de sorties (E/S), dans un boîtier intégré au processeur, à de grands dispositifs modulaires montés en rack avec un nombre de milliers d'E/S, et qui sont souvent mis en réseau avec d'autres PLC et Systèmes SCADA.
Ils peuvent être conçus pour de multiples configurations d'E/S numériques et analogiques, des plages de température étendues, une immunité au bruit électrique et une résistance aux vibrations et aux chocs.
Les programmes de contrôle du fonctionnement de la machine sont généralement stockés dans une mémoire de secours sur batterie ou non volatile.
Lorsque les ordinateurs numériques sont devenus disponibles, en tant qu'appareils programmables à usage général, ils ont rapidement été appliqués au contrôle de la logique séquentielle et combinatoire dans les processus industriels.
Comment fonctionne le PLC ?
Un contrôleur logique programmable ne peut pas fonctionner seul : il nécessite un logiciel spécial sous forme de programmes d'exploitation.
Ces programmes sont généralement écrits dans une application spéciale sur un ordinateur personnel, puis téléchargés via un câble de connexion directe ou via un réseau vers l'automate.
Le programme est stocké dans l'automate soit dans RAM avec batterie de secours ou une autre mémoire flash non volatile.
Souvent, un seul PLC peut être programmé pour remplacer des milliers de relais.
Aux premiers jours des automates programmables, les programmes étaient stockés sur des cartouches à cassette.
Les moyens d'impression et de documentation étaient minimes en raison du manque de capacité de mémoire.
Les PLC les plus anciens utilisaient une mémoire à noyau magnétique non volatile.
Plus récemment, les automates programmables sont programmés à l'aide de logiciels d'application sur des ordinateurs personnels, qui représentent désormais la logique sous forme graphique au lieu de symboles de caractères.
L'ordinateur est connecté à l'automate via USB, EthernetCâblage RS-232, RS-485 ou RS-422.
Le logiciel de programmation permet la saisie et la modification de la logique de type échelle.
Dans certains progiciels, il est également possible de visualiser et de modifier le programme sous forme de diagrammes de blocs fonctionnels, d'organigrammes de séquences et de texte structuré.
En général, le logiciel fournit des fonctions de débogage et de dépannage du logiciel PLC, par exemple en mettant en évidence des parties de la logique pour afficher l'état actuel pendant le fonctionnement ou via la simulation.
Le logiciel téléchargera et chargera le programme PLC, à des fins de sauvegarde et de restauration.
Dans certains modèles de contrôleur programmable, le programme est transféré d'un ordinateur personnel vers l'automate via une carte de programmation qui écrit le programme dans une puce amovible telle qu'un Mémoire EPROM.
Sous le Norme IEC 61131-3Les PLC peuvent être programmés à l’aide de langages de programmation basés sur des normes.
Le langage de programmation le plus couramment utilisé est le diagramme à relais (LD), également connu sous le nom de logique à relais.
Il utilise la logique Contact-Coil pour créer des programmes comme un schéma de contrôle électrique.
Une notation de programmation graphique appelée graphiques de fonctions séquentielles est disponible sur certains contrôleurs programmables.
Un modèle qui émule les dispositifs de panneau de commande électromécaniques (tels que les contacts et les bobines de relais) que les PLC remplacent.
Ce modèle reste courant aujourd'hui.
La norme IEC 61131-3 définit actuellement quatre langages de programmation pour les systèmes de contrôle programmables : le diagramme en blocs fonctionnels (FBD), le diagramme à contacts (LD), le texte structuré (ST ; similaire au langage de programmation Pascal) et le diagramme de fonctions séquentielles (SFC).
Ces techniques mettent l’accent sur l’organisation logique des opérations.
Bien que les concepts fondamentaux de la programmation PLC soient communs à tous les fabricants, les différences d'adressage des E/S, d'organisation de la mémoire et de jeux d'instructions signifient que les programmes PLC ne sont jamais parfaitement interchangeables entre les différents fabricants.
Même au sein d'une même gamme de produits d'un même fabricant, différents modèles peuvent ne pas être directement compatibles.
Quels types de boîtiers PLC KDM peut-il proposer ?
Il existe plusieurs approches pour catégoriser les boîtiers PLC.
Tout d’abord, les deux principaux types d’API sont fixes : les API compacts et les API modulaires.
L'automate compact est livré dans un seul boîtier avec de nombreux modules stockés dans un seul boîtier.
Il dispose d'un nombre fixe de modules d'E/S et de cartes d'E/S externes.
Il n’a donc pas la capacité d’étendre les modules.
Chaque entrée et sortie serait décidée par le fabricant.
L'API modulaire permet une extension multiple grâce à modules, où les composants d'E/S pourraient être augmentés.
Il est plus facile à utiliser car chaque composant est indépendant des autres.
Selon la taille physique, les boîtiers PLC peuvent être divisés en mini, micro et nano PLC.
Pouvez-vous décrire le système électrique dans lequel le boîtier PLC est utilisé ?
Les PLC sont principalement utilisés sur les sites de fabrication et industriels où l'automatisation des processus est requise.
Comme nous l'avons dit plus haut, les contrôleurs logiques programmables ont été créés pour faire fonctionner divers processus lors de la fabrication de produits automobiles, c'est-à-dire lignes d'assemblage, ou des dispositifs robotisés.
De quelles options de montage dispose-t-on avec les boîtiers PLC KDM ?
Les boîtiers PLC KDM peuvent être fournis sous les formes suivantes :
- Autoportant luminaires.
- Au sol luminaires.
- Fixation murale luminaires (y compris ceux montés sur poteau).
Pouvez-vous nommer les matériaux utilisés pour fabriquer des boîtiers PLC ?
Principalement, les spécialistes KDM utilisent inoxydable et acier au carbone pour fabriquer des boîtiers PLC.
Toutefois, si nécessaire, d’autres matériaux peuvent être utilisés (tels que divers types de plastique, fibre de verre, aluminium, etc.)
Comment tester la sécurité des boîtiers PLC contre les effets environnementaux dangereux ?
Afin de tester la capacité du boîtier à résister à la corrosion, il est exposé au gaz ammoniac.
Le ISA G3 Le test de corrosion comprenait une exposition à l'ammoniac à une concentration de 25 parties par million pendant une période continue de 30 jours.
A noter que de tels tests sont réalisés sans que l'équipement soit monté dans un boîtier (c'est à dire sans pollution directe des modules et des supports).
Cela équivaut donc à une durée de vie installée beaucoup plus longue dans une armoire, avec une exposition occasionnelle au gaz due à l'ouverture de la porte de l'enceinte, ou à une infiltration à une concentration plus faible dans l'enceinte.
De plus, le boîtier peut être testé conformément à Propriété intellectuelle et NEMA normes.
Si vous souhaitez en savoir plus sur ces tests, veuillez visiter le page suivante.
Qu'en est-il de la gestion du bruit et de la chaleur du boîtier PLC ?
La mise en œuvre des recommandations décrites précédemment devrait fournir des conditions de fonctionnement favorables pour la plupart des applications de contrôleurs programmables.
Cependant, dans certaines applications, l’environnement d’exploitation peut présenter des conditions extrêmes qui nécessitent une attention particulière.
Ces conditions défavorables comprennent un bruit et une chaleur excessifs ainsi que des fluctuations gênantes des lignes électriques.
Cette section décrit ces conditions et fournit des mesures pour minimiser leurs effets.
Bruit excessif
Le bruit électrique endommage rarement les composants PLC, sauf si des niveaux d'énergie ou de tension extrêmement élevés sont présents.
Cependant, des dysfonctionnements temporaires dus au bruit peuvent entraîner un fonctionnement dangereux de la machine dans certaines applications.
Le bruit peut être présent seulement à certains moments ou apparaître à intervalles réguliers.
Dans certains cas, elle peut exister en permanence.
Le premier cas est le plus difficile à isoler et à corriger.
Le bruit pénètre généralement dans un système par les lignes d’entrée, de sortie et d’alimentation.
Le bruit peut également être couplé électrostatiquement à ces lignes grâce à la capacité entre elles et les lignes porteuses du signal de bruit.
La présence de conducteurs à haute tension ou de conducteurs longs et rapprochés produit généralement cet effet.
Le couplage de champs magnétiques peut également se produire lorsque les lignes de commande sont situées à proximité de lignes transportant des courants importants.
Les dispositifs susceptibles de générer du bruit comprennent les relais, les solénoïdes, les moteurs et les démarreurs de moteur, en particulier lorsqu'ils sont actionnés par des contacts durs, tels que des boutons-poussoirs et des commutateurs sélecteurs.
Les E/S analogiques et les émetteurs sont très sensibles au bruit provenant de sources électromécaniques, provoquant des sauts de comptage lors de la lecture des données analogiques.
Par conséquent, les démarreurs de moteur, les transformateurs et autres appareils électromécaniques doivent être tenus à l’écart des signaux analogiques, des interfaces et des émetteurs.
Bien que la conception des commandes à semi-conducteurs offre une immunité au bruit raisonnable, le concepteur doit néanmoins prendre des précautions particulières pour minimiser le bruit, en particulier lorsque le signal de bruit prévu présente des caractéristiques similaires aux signaux d'entrée de commande souhaités.
Pour augmenter la marge de bruit de fonctionnement, le contrôleur doit être installé loin des appareils générateurs de bruit, tels que les gros moteurs à courant alternatif et les machines à souder haute fréquence.
De plus, toutes les charges inductives doivent être supprimées.
Les fils du moteur triphasé doivent être regroupés et acheminés séparément des fils de signal de bas niveau.
Parfois, si le niveau de bruit est critique, tous les fils du moteur triphasé doivent être supprimés.
Chaleur excessive
Les contrôleurs programmables peuvent supporter des températures allant de 0 à 60°C.
Ils sont normalement refroidis par convection, ce qui signifie qu'une colonne d'air verticale, aspirée vers le haut sur la surface des composants, refroidit l'automate.
Pour maintenir la température dans les limites, le air de refroidissement à la base du système ne doit pas dépasser 60°C.
Les composants du PLC doivent être correctement espacés lors de leur installation pour éviter un excès de chaleur.
Le fabricant peut fournir des recommandations d'espacement, basées sur des conditions typiques pour la plupart des applications PLC.
Les conditions typiques sont les suivantes :
- 60% des entrées sont ON à tout moment ;
- 30% des sorties sont ON à tout moment ;
- le courant fourni par l'ensemble des modules combinés est conforme aux spécifications fournies par le fabricant ;
- la température de l'air est d'environ 40°C.
Les situations dans lesquelles la plupart des E/S sont activées en même temps et la température de l'air est supérieure à 40 °C ne sont pas typiques.
Dans ces situations, l’espacement entre les composants doit être plus grand pour assurer un meilleur refroidissement par convection.
Si l'équipement à l'intérieur ou à l'extérieur du boîtier génère des quantités importantes de chaleur et que le système d'E/S est allumé en permanence, le boîtier doit contenir un ventilateur cela réduira les points chauds à proximité du système PLC en assurant une bonne circulation de l'air.
L'air amené par le ventilateur doit d'abord passer à travers un filtre pour empêcher la saleté ou d'autres contaminants de pénétrer dans l'enceinte.
La poussière obstrue la capacité de dissipation thermique des composants et endommage les dissipateurs thermiques lorsque la conductivité thermique de l'air ambiant est réduite.
En cas de chaleur extrême, l'enceinte doit être équipée d'un climatiseur ou d'un système de contrôle de refroidissement utilisant de l'air comprimé.
Laisser les portes du boîtier ouvertes pour refroidir le système n’est pas une bonne pratique car cela permet à la poussière conductrice de pénétrer dans le système.
Dois-je vérifier les conditions du PLC avant de le démarrer ?
Avant de mettre le système sous tension, l’utilisateur doit effectuer plusieurs inspections finales des composants matériels et des interconnexions.
Ces inspections nécessiteront sans doute du temps supplémentaire.
Cependant, ce temps investi réduira presque toujours le temps de démarrage total, en particulier pour les grands systèmes dotés de nombreux périphériques d'entrée/sortie.
La liste de contrôle suivante concerne les procédures de pré-démarrage :
- Inspectez visuellement le système pour vous assurer que tous Matériel PLC les composants sont présents. Vérifiez les numéros de modèle corrects pour chaque composant.
- Inspectez tous les composants du processeur et les modules d'E/S pour vous assurer qu'ils sont installés dans les emplacements appropriés et qu'ils sont bien placés en place.
- Vérifiez que l’alimentation entrante est correctement câblée à l’alimentation (et au transformateur) et que l’alimentation du système est correctement acheminée et connectée à chaque rack d’E/S.
- Vérifiez que les câbles de communication d'E/S reliant le processeur aux racks d'E/S individuels correspondent à l'attribution d'adresse du rack d'E/S.
- Vérifiez que toutes les connexions de câblage d'E/S côté contrôleur sont en place et correctement raccordées. Utilisez le document d'attribution d'adresses d'E/S pour vérifier que chaque fil est raccordé au bon endroit.
- Vérifiez que les connexions de câblage de sortie sont en place et correctement terminées à l'extrémité de l'appareil de terrain.
- Assurez-vous que la mémoire système a été vidée des programmes de contrôle précédemment stockés. Si le programme de contrôle est stocké dans l'EPROM, retirez temporairement les puces.
Vérification du câblage d'entrée statique
Une vérification du câblage d'entrée statique doit être effectuée avec l'alimentation appliquée au contrôleur et aux périphériques d'entrée.
Cette vérification permettra de vérifier que chaque périphérique d'entrée est connecté au bon borne d'entrée et que les modules ou points d’entrée fonctionnent correctement.
Étant donné que ce test est effectué avant les autres tests du système, il permettra également de vérifier que le processeur et le dispositif de programmation sont en bon état de fonctionnement.
Le câblage d'entrée approprié peut être vérifié à l'aide des procédures suivantes :
- Placez le contrôleur dans un mode qui empêchera l'automate de fonctionner automatiquement. Ce mode varie en fonction du modèle d'automate, mais il s'agit généralement d'un mode d'arrêt, de désactivation, de programmation, etc.
- Mettez sous tension l'alimentation du système et les périphériques d'entrée. Vérifiez que tous les systèmes indicateurs de diagnostic afficher le bon fonctionnement. Les indicateurs typiques sont AC OK, DC OK, processeur OK, mémoire OK et communication E/S OK.
- Vérifiez que le circuit d’arrêt d’urgence coupera l’alimentation des périphériques d’E/S.
- Activez manuellement chaque périphérique d'entrée. Surveillez l'indicateur d'état LED correspondant sur le module d'entrée et/ou surveillez l'utilisation de la même adresse sur le périphérique de programmation. S'il est correctement câblé, l'indicateur s'allume. Si un indicateur autre que celui prévu s'allume lorsque le périphérique d'entrée est activé, le périphérique d'entrée peut être câblé sur la mauvaise borne d'entrée. Si aucun indicateur ne s'allume, il peut y avoir un défaut dans le périphérique d'entrée, le câblage sur site ou le module d'entrée
- Prenez des précautions pour éviter les blessures ou les dommages lors de l'activation de périphériques d'entrée connectés en série avec des charges externes à l'API.
Vérification du câblage de sortie statique
Une vérification du câblage de sortie statique doit être effectuée avec l'alimentation appliquée au contrôleur et aux périphériques de sortie.
Une pratique sûre consiste à déconnecter d'abord localement tous les périphériques de sortie qui impliquent un mouvement mécanique (par exemple, moteurs, solénoïdes, etc.).
Une fois effectué, le contrôle du câblage de sortie statique vérifiera que chaque périphérique de sortie est connecté à l'adresse de terminal correcte et que le périphérique et le module de sortie fonctionnent correctement.
Les procédures suivantes doivent être utilisées pour vérifier le câblage de sortie :
- Déconnecter localement tout périphériques de sortie cela provoquera un mouvement mécanique.
- Appliquez l'alimentation au contrôleur et aux périphériques d'entrée/sortie. Si un arrêt d'urgence peut couper l'alimentation des sorties, vérifiez que le circuit coupe l'alimentation lorsqu'il est activé.
- Effectuez le contrôle statique des sorties une par une. Si la sortie est un moteur ou un autre appareil qui a été déconnecté localement, remettez l'alimentation sur cet appareil uniquement avant de procéder au contrôle. Le contrôle du fonctionnement des sorties peut être effectué à l'aide de l'une des méthodes suivantes :
- En supposant que le contrôleur dispose d'une fonction de forçage, testez chaque sortie, à l'aide du dispositif de programmation, en forçant la sortie à ON et en définissant l'adresse de borne correspondante (point) sur 1. Si le câblage est correctement effectué, le voyant LED correspondant s'allumera et le dispositif sera mis sous tension. Si un indicateur autre que celui prévu s'allume lorsque l'adresse de borne est forcée, le dispositif de sortie peut être câblé sur la mauvaise borne de sortie (le fonctionnement involontaire de la machine ne se produit pas car les sorties rotatives et autres sorties génératrices de mouvement sont déconnectées). Si aucun indicateur ne s'allume, il peut y avoir un défaut dans le dispositif de sortie, le câblage de terrain ou le module de sortie.
- Programmez un échelon factice, qui peut être utilisé de manière répétée pour tester chaque sortie, en programmant un seul échelon avec un seul contact normalement ouvert (par exemple, un bouton-poussoir bien placé) contrôlant la sortie. Placez le processeur en mode RUN, en mode single-scan ou dans un mode similaire, selon le contrôleur. Avec le contrôleur en mode RUN, appuyez sur le bouton-poussoir pour effectuer le test. Avec le contrôleur en mode single-scan, appuyez sur le bouton-poussoir et maintenez-le enfoncé pendant que le contrôleur exécute le single-scan. Observez le périphérique de sortie et le voyant LED, comme décrit dans la première procédure.
Examen du programme de contrôle
La vérification du programme de contrôle est simplement un examen final de l' programme de contrôle.
Cette vérification peut être effectuée à tout moment, mais elle doit être effectuée avant de charger le programme en mémoire pour la vérification dynamique du système.
Pour effectuer la vérification du programme de contrôle, un package de documentation complet reliant le programme de contrôle aux appareils de terrain réels est nécessaire.
Des documents, tels que des attributions d'adresses et schémas de câblage, doit refléter toutes les modifications qui ont pu survenir lors des contrôles du câblage statique.
Une fois effectuée, cette révision finale du programme permettra de vérifier que la copie papier finale du programme, qui sera chargée en mémoire, est exempte d'erreurs ou au moins conforme aux documents de conception originaux.
Voici une liste de contrôle pour la vérification du programme de contrôle final :
- À l’aide de l’impression du document de câblage des E/S, vérifiez que chaque périphérique de sortie contrôlé dispose d’un échelon de sortie programmé de la même adresse.
- Inspectez la copie papier pour détecter d'éventuelles erreurs qui auraient pu se produire lors de la saisie du programme. Vérifiez que tous les contacts du programme et les sorties internes ont des adresses attribuées valides.
- Vérifiez que toutes les valeurs de minuterie, de compteur et autres valeurs prédéfinies sont correctes.
Vérification du système dynamique
Le contrôle dynamique du système est une procédure qui vérifie la logique du programme de contrôle pour garantir le bon fonctionnement des sorties.
Cette vérification suppose que tous les contrôles statiques ont été effectués, que le câblage est correct, que les composants matériels sont opérationnels et fonctionnent correctement et que le logiciel a été soigneusement examiné.
Lors du contrôle dynamique, il est possible de mettre progressivement le système sous contrôle entièrement automatique.
Bien que les petits systèmes puissent être démarrés tous en même temps, un grand système doit être démarré par sections.
Les grands systèmes utilisent généralement des sous-systèmes distants qui contrôlent différentes sections de la machine ou du processus.
La mise en ligne d'un sous-système à la fois permet à l'ensemble du système de démarrer avec une sécurité et une efficacité maximales.
Les sous-systèmes distants peuvent être temporairement désactivés soit en supprimant localement leur alimentation, soit en déconnectant leur liaison de communication avec le processeur.
Les pratiques suivantes décrivent les procédures de vérification du système dynamique :
- Chargez le programme de contrôle dans la mémoire de l'API.
- Testez la logique de contrôle en utilisant l’une des méthodes suivantes :
- Basculez le contrôleur en mode TEST, si disponible, ce qui permettra l'exécution et le débogage du programme de contrôle pendant que les sorties sont désactivées. Vérifiez chaque échelon en observant l'état des indicateurs LED de sortie ou en surveillant l'échelon de sortie correspondant sur le dispositif de programmation.
- Si le contrôleur doit être en mode RUN pour mettre à jour les sorties pendant les tests, déconnectez localement les sorties qui ne sont pas testées, pour éviter tout dommage ou préjudice. Si une instruction MCR ou similaire est disponible, utilisez-la pour contourner l'exécution des sorties qui ne sont pas testées, de sorte que la déconnexion des périphériques de sortie ne soit pas nécessaire.
- Vérifiez le bon fonctionnement logique de chaque échelon et modifiez la logique si nécessaire. Un outil utile pour déboguer la logique de contrôle est l'analyse unique. Cette procédure permet à l'utilisateur d'observer chaque échelon au fur et à mesure de l'exécution de chaque analyse.
- Lorsque les tests indiquent que toute la logique contrôle correctement les sorties, retirez tous les échelons temporaires qui ont pu être utilisés (MCR, etc.). Placez le contrôleur en mode RUN et testez le fonctionnement global du système. Si toutes les procédures sont correctes, le contrôle entièrement automatique devrait fonctionner sans problème.
- Documentez immédiatement toutes les modifications apportées à la logique de contrôle et révisez la documentation d'origine. Obtenez une copie reproductible du programme dès que possible.
Comment entretenir efficacement le boîtier et les composants internes d'un PLC ?
Les contrôleurs programmables sont conçus pour être faciles à entretenir, afin de garantir un fonctionnement sans problème.
Néanmoins, plusieurs aspects de maintenance doivent être pris en compte une fois le système en place et opérationnel.
Certaines mesures, si elles sont appliquées périodiquement, minimiseront les risques de dysfonctionnement du système.
Cette section décrit certaines des pratiques à suivre pour maintenir le système en bon état de fonctionnement.
La maintenance préventive des systèmes de contrôleurs programmables ne comprend que quelques procédures de base, qui réduiront considérablement le taux de défaillance des composants du système.
La maintenance préventive du système PLC doit être programmée avec la maintenance régulière de la machine ou de l'équipement afin que l'équipement et le contrôleur soient hors service pendant un minimum de temps.
Cependant, le calendrier de maintenance préventive du PLC dépend de l'environnement du contrôleur : plus l'environnement est difficile, plus la maintenance est fréquente.
Voici quelques lignes directrices concernant les mesures préventives :
- Nettoyez ou remplacez régulièrement les filtres installés dans les enceintes à une fréquence qui dépend de la quantité de poussière présente dans la zone. N'attendez pas la maintenance programmée de la machine pour vérifier le filtre. Cette pratique permettra de garantir une circulation d'air propre à l'intérieur de l'enceinte.
- Ne laissez pas la saleté et la poussière s'accumuler sur les composants de l'automate ; l'unité centrale de traitement et le système d'E/S ne sont pas conçus pour être étanche à la poussière. Si de la poussière s'accumule sur les dissipateurs thermiques et les circuits électroniques, elle peut entraver la dissipation de chaleur et provoquer un dysfonctionnement du circuit. De plus, si de la poussière conductrice atteint les cartes électroniques, elle peut provoquer un court-circuit, ce qui peut entraîner des dommages permanents sur la carte de circuit imprimé.
- Vérifiez régulièrement les connexions aux modules d'E/S pour vous assurer que toutes les fiches, prises, borniers et modules sont correctement connectés. Vérifiez également que le module est correctement installé. Effectuez ce type de contrôle plus souvent lorsque le système PLC est situé dans une zone soumise à des vibrations constantes, qui pourraient desserrer les connexions des bornes.
- Assurez-vous que les équipements lourds et générateurs de bruit ne sont pas situés trop près de l'automate. Assurez-vous que les éléments inutiles sont tenus à l'écart de l'équipement à l'intérieur du boîtier. Le fait de laisser des éléments, tels que des dessins, des manuels d'installation ou d'autres documents, sur le rack du processeur ou d'autres boîtiers de rack peut obstruer la circulation de l'air et créer des points chauds, ce qui peut entraîner un dysfonctionnement du système.
- Si le boîtier du système PLC se trouve dans un environnement soumis à des vibrations, installez un détecteur de vibrations pouvant s'interfacer avec le PLC à titre préventif. De cette façon, le contrôleur programmable peut surveiller des niveaux de vibrations élevés, qui peuvent entraîner le desserrage des connexions.
Il est judicieux de conserver un stock de pièces de rechange à disposition.
Cette pratique minimisera les temps d’arrêt résultant d’une défaillance d’un composant.
En cas de panne, disposer d'une pièce de rechange adéquate en stock peut signifier un arrêt de quelques minutes seulement, au lieu de plusieurs heures ou jours.
En règle générale, la quantité d'une pièce de rechange stockée doit être de 10% du nombre de cette pièce utilisée.
Si une pièce est utilisée peu fréquemment, moins de 10% de cette pièce particulière peuvent être stockées.
Les principaux composants de la carte CPU doivent chacun avoir un composant de rechange, quel que soit le nombre de processeurs utilisés.
Chaque alimentation, qu'elle soit principale ou auxiliaire, doit également disposer d'une alimentation de secours.
Certaines applications peuvent nécessiter une Support de processeur comme pièce de rechange de secours.
Ce cas extrême se produit lorsqu'un système en panne doit être remis en service immédiatement, sans laisser le temps de déterminer quelle carte CPU est défaillante.
Si un module doit être remplacé, l'utilisateur doit s'assurer que le module de remplacement installé est du bon type.
Certains systèmes d'E/S permettent de remplacer des modules alors que l'alimentation est toujours appliquée, mais d'autres peuvent nécessiter que l'alimentation soit coupée.
Si le remplacement d’un module résout le problème, mais que la panne se reproduit dans une période relativement courte, l’utilisateur doit vérifier les charges inductives.
Les charges inductives peuvent générer des pics de tension et de courant, auquel cas une suppression externe peut être nécessaire.
Si le fusible du module saute à nouveau après son remplacement, le problème peut être dû au dépassement de la limite de courant de sortie du module ou au court-circuit du périphérique de sortie.
Commande récente de boîtier PLC
Boîtiers PLC
Les boîtiers PLC sont des armoires utilisées pour les panneaux de contrôle industriels et les processeurs internes. Ils préservent les PLC et autres composants électroniques sensibles dans d'excellentes conditions. Ce boîtier protège les techniciens du contact avec les pièces sous tension.
Boîtiers PLC
Le boîtier PLC garantit une durabilité à long terme. Il peut contribuer au bon fonctionnement de tous les composants sécurisés.
Quelles sont les applications des boîtiers PLC ?
Les boîtiers PLC sont spécialement conçus pour fonctionner parfaitement dans les applications intérieures et extérieures. Que ce soit pour la distribution d'énergie électrique ou l'ingénierie, les boîtiers PLC fonctionnent parfaitement. Ils s'appliquent généralement dans :
- lignes de fabrication
- systèmes de convoyeurs
- raffineries de pétrole
- automatisation intérieure et extérieure
Quelles pièces contient le boîtier PLC ?
- alimentations électriques
- routeurs
- commutateurs
- microcontrôleurs
- câblages électriques
- appareils à fibre optique
- autres parties.
Les boîtiers PLC protègent l'électronique contre:
- températures élevées
- humidité
- humidité
- poussière, eau, huile
- chocs et vibrations
- forces mécaniques
- environnements corrosifs.
Quels éléments peuvent réduire la durée de vie des boîtiers PLC ?
La surchauffe et l'humidité affectent la durée de vie de vos boîtiers PLC. Elles peuvent entraîner des pannes système majeures. Elles peuvent également entraîner un risque de décharge électrique pour les opérateurs.
Quels aspects doivent être pris en compte lors du choix des bons matériaux pour les boîtiers PLC ?
Le boîtier de l'automate doit être assemblé à partir des meilleurs matériaux. Il doit offrir :
- résistance aux intempéries
- sécurité incassable
- résistance aux chocs
- résistance aux rayures
- résistance à la corrosion
- Protection contre les rayons UV
- protection de température
Quels matériaux sont utilisés dans la production de boîtiers PLC ?
Le choix du bon matériau pour vos boîtiers PLC joue un rôle essentiel dans leur durabilité et leur longévité. Voici quelques-uns des matériaux utilisés dans la fabrication des boîtiers PLC :
Acier – l’acier est un matériau solide adapté à la fabrication de boîtiers PLC. Parmi ses avantages, on peut citer sa polyvalence et sa flexibilité. Il est résistant au feu et aux intempéries. Ce matériau peut améliorer la qualité de construction.
Acier galvanisé – Les boîtiers PLC en acier galvanisé sont dotés d'un revêtement durable. Il offre une protection complète aux composants électriques. Ce matériau offre moins d'entretien et est respectueux de l'environnement.
Acier inoxydable - Les boîtiers PLC en acier inoxydable ont une esthétique propre et élégante. Il offre une grande résistance à la rouille et à la corrosion. L'acier inoxydable est connu pour sa résistance aux chocs et ses caractéristiques de solidité. Il est facile à nettoyer et à entretenir. Mais c'est un matériau lourd et plus cher que les autres matériaux.
Aluminium – Les boîtiers PLC en aluminium sont durables. Ils peuvent supporter des températures élevées. Ils sont également résistants à la corrosion et à la rouille. Ils sont plus chers que les boîtiers PLC en plastique.
Acier au carbone – Les boîtiers PLC en acier au carbone sont abordables et rigides. Mais malheureusement, ce matériau est sujet à la rouille. Vous devez d'abord tenir compte de l'application avant de choisir ce matériau.
Plastique polycarbonate – Le boîtier PLC en plastique polycarbonate est moins cher que les autres matériaux mentionnés ci-dessus. En raison de ses caractéristiques de résistance aux UV, il convient aux applications extérieures. Ce matériau offre une meilleure résistance aux chocs.
Que faut-il prendre en compte avant d’acheter des boîtiers PLC ?
Matériaux de l'enceinte
Si vous choisissez un boîtier PLC fabriqué à partir de matériaux de haute qualité, vous pouvez être sûr d'une utilisation durable. L'acier inoxydable, l'aluminium et l'acier galvanisé sont quelques-unes des meilleures options pour ce boîtier.
Dimensions du boîtier
Faites attention aux dimensions ou aux tailles du boîtier de l'automate. La dimension des boîtiers dépendra de l'équipement que vous monterez à l'intérieur. Il peut être conçu avec une profondeur de 16 à 20 pouces, une hauteur de 62 à 78 pouces et une largeur de 23 à 31 pouces.
Compatibilité du boîtier
Tenez compte de la compatibilité de vos boîtiers avec votre équipement électrique. Vérifiez si l'équipement est prévu pour être monté à l'intérieur.
Fonction de l'enceinte
Les boîtiers PLC ont de nombreuses fonctions. Assurez-vous de savoir ce que vous souhaitez obtenir avec le boîtier. Certaines entreprises préfèrent les boîtiers PLC pour protéger leur équipement électrique. Tandis que d'autres l'utilisent pour garder leurs commandes en ordre. Il est également doté de fonctionnalités pratiques en fonction des aspects spécifiques dont vous avez besoin.
Demande de clôture
Vous devez vous assurer de l'application à laquelle votre boîtier est destiné. En fonction de l'application du boîtier, le fabricant peut déterminer le boîtier PLC le mieux adapté à vos besoins.
Protection de l'enceinte
Les boîtiers PLC doivent être conformes aux normes NEMA et aux systèmes de classification IP. Ils garantissent une excellente protection contre les dangers des applications industrielles.
Des boîtiers PLC personnalisés sont-ils disponibles ?
Oui, bien sûr. De nombreux fabricants fournissent des spécifications personnalisées pour répondre aux exigences de vos boîtiers PLC, telles que :
- largeur
- profondeur
- couleurs
- espace de rack
- modèles de portes
- options verrouillables
- choix de panneaux
- revêtement/finition en poudre
- notes de certification
Quelles sont les caractéristiques des boîtiers PLC ?
Caractéristiques des boîtiers PLC
Les boîtiers PLC présentent des caractéristiques uniques. Ils sont adaptés à vos besoins spécifiques. Voici quelques-uns des avantages des boîtiers PLC :
Flexibilité
Les boîtiers PLC sont conçus pour offrir une certaine flexibilité. Ils sont peu encombrants et peuvent s'adapter à l'espace dont vous disposez.
Facilité d'accès
Vous pouvez accéder facilement à vos composants électroniques et à votre câblage grâce aux boîtiers PLC. Cela permet une utilisation optimale de vos composants électriques. Ce boîtier est doté d'une conception de gestion des câbles ou des fils facile. Il peut être conçu avec un petit écran pour surveiller ou contrôler les processus et un bouton marche/arrêt rapide sur la porte.
Qualité supérieure
Les boîtiers PLC sont fabriqués à partir de composants durables et fiables.
Efficacité améliorée
Les boîtiers PLC offrent une efficacité améliorée à votre électronique.
Rentable
L'utilisation de boîtiers en acier peut vous permettre de réaliser des économies en raison de leurs besoins de maintenance réduits. Le boîtier PLC durera plus longtemps. Vous pouvez économiser de l'argent en achetant un autre boîtier.
Écologique et recyclable
Lorsque le boîtier de l'automate atteint sa durée de vie, vous pouvez le recycler. Il peut être transformé en un nouveau boîtier d'automate. Les boîtiers d'automate sont faciles à nettoyer et à entretenir. Ainsi, diverses installations de traitement et de fabrication les utilisent.
Installation facile
L'installation d'un boîtier PLC est rapide et facile.
Sûr et durable
Les boîtiers PLC sont sûrs et polyvalents. Ils sont sûrs pour la manipulation par l'opérateur.
Il peut résister à divers éléments tels que la corrosion, les parasites et le feu. Il peut supporter des conditions difficiles, notamment des températures extrêmement chaudes et des climats humides.
Protection nominale NEMA
Boîtiers PLC, classifications NEMA
La norme de classification NEMA nous indique les types d'environnements dans lesquels les boîtiers PLC peuvent être utilisés. Elle peut améliorer la fiabilité et la sécurité de ces produits.