KDM is acknowledged as one of the leading suppliers, manufacturers, and exporters of all kinds of sheet metal parts.
Along with our experienced and skilled professionals
Professional Sheet Metal Fabrication Factory in China
KDM has manufactured high-quality sheet metal parts with our latest equipment and advanced machines during production. Our sheet metal parts are mainly used in allied industries, engineering, and automobile. These sheet metal parts are popular for their advantageous features such as minimum maintenance, user-friendly design, and easy installation. In addition to this, a qualitative range of sheet metal parts can be used in passenger vehicles as well as in many commercial.
- High-quality, superior performance, timely delivery and cost-effectiveness Sheet Metal Parts.
- Long functional life sheet metal parts for trimming, punching, cutting, etc.
- Ease of maintenance and installation, long-lasting surface finish, and unique strength
- Fully customization of sheet metal parts according to your drawings
The sheet metal parts from KDM are dimensionally accurate and fabricated using advanced CNC machines. For that reason, it makes perfect for car bodies component and another component of essential engines.
The durability and superior surface finish of the sheet metal parts allow them to use in transmissions, brake linings, heat exchanger and many more. What’s more, KDM sheet metal parts are popular by the customers for its rust resistance, abrasion, breakage and more. Our offered products are in compliance with the industry set standard and manufactured using certified quality components.
KDM Sheet Metal Parts Series
Our sheet metal prototype parts are widely known for their superior performance, high-quality, timely delivered and cost-effectiveness.
Are you looking for a certified manufacturer and supplier of precious sheet metal parts? Always count on KDM. We provide a supreme quality of all sheet metal part types.
A qualitative range of sheet metal turn parts is mainly used in passenger vehicles and as well as in many commercial. It is highly demanded and appreciated by most client for itsrust resistance, abrasion, breakage and more.
Send your Inquiry on KDM Sheet Metal Parts
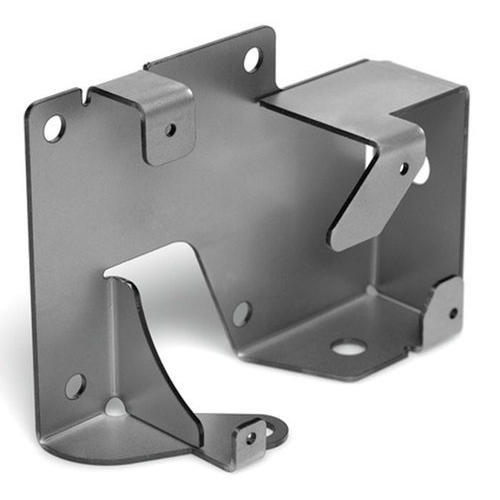
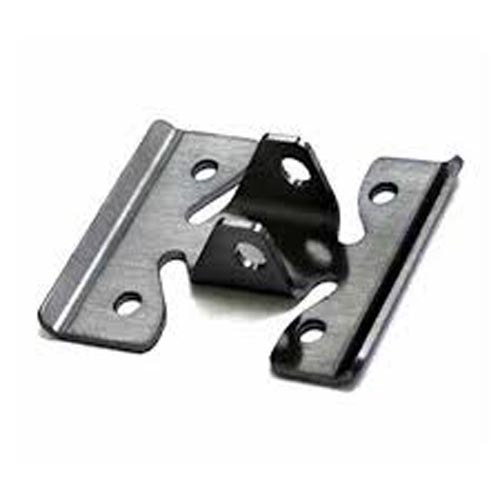
As a reliable and reputed supplier, exporter and manufacturer in this industry, KDM is actively committed to supplying the highest quality sheet metal part to our valued customers.Our sheet metal parts are engineered and developed under the specification of expert professionals.
Related Products of Sheet Metal Parts
KDM Sheet Metal Parts
In our factory, our KDM sheet metal parts can be available in various specifications.
We have sheet metal parts which are developed from high-grade copper or stainless steel.
These parts are used in industrial equipment.
Outstanding for their compact shape, KDM sheet metal parts are calculated for their corrosion and good wear performance, abrasion-proof design, ease of maintenance and installation, long-lasting surface finish, and unique strength.
KDM sheet metal parts are tested on the premise of their service life, surface hardness level, and dimensional accuracy.
The offered products have been fabricated by using technical knowledge and the latest equipment.
Constructed with the furthest exactness, this range of KDM sheet metal parts is widely utilized as extra parts and car parts.
This wide array is refreshing for erosion safe nature, traits, for example, longer functional life and dimensional exactness.
Committed to exceeding the expectations and needs of our valued clients, KDM are involved in supplying sheet metal parts throughout the world.
KDM sheet metal parts include couplings, Electrical Wire Chase, fasteners and brass glands available in different specifications.
The offered products are ideally suited for different purposes like trimming, punching, cutting, etc.
It is highly demanded in the market for its high-quality, superior performance, timely delivered and cost-effectiveness.
Clients can avail KDM sheet metal parts in varied finishes and sizes with the required amount at a market leading price. Contact us right away!
Sheet metal parts: The Complete FAQ Guide
There are a lot of ways to prepare metal for various manufacturing purposes.
One of such methods is making a sheet metal that can be later used in different industries, such as automotive, construction industry, and many others.
But what are the main advantages that make us use such type of metal in our economy?
دعونا نكتشف ذلك.
- What are sheet metal parts?
- What is a sheet metal blank?
- What kind of materials are used to produce sheet metal parts?
- What kind of sheet metal parts can KDM manufacture?
- What is a gauge?
- What are the main advantages of sheet metal parts?
- How sheet metal parts are made?
- How to design sheet metal parts?
- What is the maximum thickness of sheet metal?
- What is the standard size of sheet metal?
- What is nesting in sheet metal parts manufacturing?
- How to strengthen sheet metal parts? What are the main methods?
- What are the tolerances on sheet metal parts?
- What is the difference between coated and non-coated parts in sheet metal?
- What kind of fasteners are used with sheet metal?
- How to inspect sheet metal parts?
- How to stamp sheet metal parts?
- What is the K factor in sheet metal? What is the difference between the K factor and Y factor?
- What is a joggle in sheet metal?
- Can KDM sheet metal parts be used for cars and trucks?
- What is the HS code of sheet metal parts?
- How to estimate costs when buying sheet metal parts?
- Galvanized sheet metal parts: what are they?
- How long does it take to get an answer from you?
- Can I require a sample of sheet metal from KDM?
- How much time is needed for KDM to fulfill my sheet metal parts order?
What are sheet metal parts?
Sheet metal is a type of metal that goes through special foaming procedures to become thin and flat pieces.
So, sheet metal parts are any kind of products made from sheet metal.
We’ll dig deeper into the topic of industries where such parts can be used later in this article.
What is a sheet metal blank?
In order to improve the speed of manufacturing, KDM uses blanks to fulfill low quantity orders.
A blank (the flat version of your part) can be cut from a sheet using a special laser or punching technique, and then bent to the needed shape using a brake press.
Sheet metal blanks are mainly used to save time and be sure that KDM can fulfill the vast majority of orders right after they come in.
What kind of materials are used to produce sheet metal parts?
KDM uses aluminum and stainless steel to produce sheet metal parts.
Speaking of the stainless steel, there are two families used to fabricate sheet metal – standard and spring-like.
Standard الفولاذ المقاوم للصدأ (Grade 300) is commonly non-magnetic and is the most commonly used type of stainless.
It does not require hot work or other stress relief during manufacturing.
Grade 316 has the best corrosion-resistant properties and maintains its strength at high temperatures.
Grade 304 is the most widely used and, while it is somewhat less corrosion-resistant, offers good weldability, as well as formability.
If you see stainless steel of 400 series, it means that it is a standard type of magnetic stainless for sheet metal fabrication.
Grade 410 offers less corrosion resistance but can be treated with heat.
Grade 430 is the most inexpensive alternative to the other stainless steel types and is used in applications where corrosion resistance is not a major requirement such as brush-finished appliance surfaces.
Because these materials tend toward elastic deformation, they must be over bent to achieve the final form.
Spring-like steels will work-harden quickly and must be heated to relieve stresses when being formed.
Spring-like stainless steel typically requires specialized equipment and processes and must be over bent to achieve the final form.
Aluminum is also a popular metal used in sheet metal manufacturing due to its flexibility, wide range of options, cost-effectiveness, and other useful properties.
The four most common aluminum grades available as sheet metal are 1100-H14, 3003-H14, 5052-H32, and 6061-T6.
The main difference between aluminum and steel lies in the properties of these materials: steel is stronger but aluminum is more flexible.
What kind of sheet metal parts can KDM manufacture?
Our specialists are able to fulfill all the imaginable orders when it comes to sheet metal parts.
Our pieces can be used to produce machinery, various enclosures, cabinets, and any other products where the thin metal is needed.
What is a gauge?
A sheet metal gauge (sometimes spelled “gage”) is a value that indicates the standard thickness of sheet metal for a certain material.
The bigger the gauge number, the thicker the material is.
Sheet metal thickness gauges for steel are based on a weight of 41.82 pounds per square foot per inch of thickness.
You can see standards gauge numbers in the picture below.
What are the main advantages of sheet metal parts?
There are a lot of reasons why it is better to use sheet metal in various economy areas.
Here are some of them:
- Sheet metal has quite a low weight, which means it’s easy to transport and easy to work with.
- Sheet metal is extremely strong, durable, and can withstand various environmental effects. This makes it the ideal high-strength material in a diversity of applications from harsh agricultural environments (e.g. sheep feeders and wheat bins) and high traffic environments (e.g. stair treads or metal scaffold planking) to extreme temperatures (e.g. industrial washing machines and ovens).
- Sheet metal can be easily formed, cut, bent or stretched into practically any shape, allowing sheet metal fabricators to offer their customers highly specialized solutions and custom-designs for any imaginable application.
- Sheet metal can also be used for repairing.
- Its relatively low cost is also an advantage in both one-off design situations and in situations involving large quantities for mass production.
How sheet metal parts are made?
The sheet metal itself is made by taking a large cast ingot and rolling it into a long ribbon of the desired thickness.
This long, flat piece of metal is then rolled into a coil and sent directly or cut into sheets.
There are a lot of techniques of further treatment of sheet metal that are used to get the needed parts:
- Bending (manufacturing process that produces a V-shape, U-shape, or channel shape pieces of metal).
- Curling (this procedure is used to form edges and remove sharp particles from them).
- Decambering (a metalworking process of removing camber and the horizontal bend, from a piece of sheet metal).
- Deep drawing (it is a forming process in which the metal is stretched over a die or some kind of a form).
- Expanding (manufacturing process of cutting or stamping slits in a certain pattern and then stretching the sheet open in accordion-like style).
- Hemming and seaming (hemming is needed to fold the edge of sheet metal onto itself to reinforce that edge, while seaming is a process of folding two sheets of metal together to form a joint).
- Hydroforming (it is a process similar to deep drawing, in that the part is formed by stretching the blank over a stationary die. The required force is generated by the direct application of extremely high hydrostatic pressure to the blank).
- Ironing (this process can be used to make some parts of blank thinner and produce a uniform wall thickness part with a high height-to-diameter ratio).
- Laser cutting (the process in which the blank is heated and burnt by the laser beam, cutting it in needed places).
- Photochemical machining (it is a tightly controlled corrosion process which is used to produce complex metal parts from sheet metal).
- Perforating (this is a cutting process that punches multiple small holes close together).
- Press brake forming (basically, this is a form of bending used to produce long, thin sheet metal parts).
- Punching (such procedure is performed by placing the sheet of metal between a punch and a die mounted in a press).
- Roll forming (it is a continuous bending operation for producing open profiles or welded tubes with long lengths or in large quantities).
- Rolling (in this case, the blank is passed through one or more pairs of rolls to reduce the thickness and make it uniform).
- Spinning (is used to make tubular parts by fixing a piece of sheet metal to a rotating form that presses the blank and stretches it until the blank takes the shape of the form).
- Water jet cutting (a waterjet is a tool capable of a controlled erosion into metal or other materials using a jet of water at high velocity and pressure).
Using the above-mentioned techniques, KDM is able to produce practically all the imaginable sheet metal parts.
How to design sheet metal parts?
Sheet metal parts can be designed both manually or with the help of computer programs.
This is a very important part of sheet metal manufacturing because initial blueprints will be used precisely and if they contain mistakes, the end-product might not meet your expectations as well.
If you can’t make a drawing on your own, you can require the help of KDM specialists.
What is the maximum thickness of sheet metal?
The thicknesses of sheet metal can differ significantly.
For example, extremely thin sheets are considered foil, and pieces thicker than 6 mm are considered plate steel.
What is the standard size of sheet metal?
To make the manufacturing processes cost-effective, it is important to use as much raw material as possible.
Thus, we avoid tons of scrap and help the environment meanwhile.
To do so, KDM engineers design parts that can easily fit within standard sheet sizes.
Here is a list of such standard sizes:
- 36 x 96 inches;
- 36 x 120 inches;
- 36 x 144 inches;
- 48 x 96 inches;
- 48 x 120 inches;
- 48 x 144 inches;
These are standard for most steel and aluminum pieces.
What is nesting in sheet metal parts manufacturing?
Nesting also refers to the process of minimizing the waste of raw material.
It is a process of creating the right cutting patterns to make as many useful parts as possible.
These efforts can be applied to additive manufacturing as well (e.g. 3D printing).
How to strengthen sheet metal parts? What are the main methods?
Sheet metal can be made stronger with the help of the following procedures.
# 1. Holes and slots punching
The sheet metal can be strengthened by punching holes and slots in the blank.
The metal in the areas where holes and slots are punched gets stretched and becomes more tensile which gives more structural rigidity to the whole piece.
# 2. Wire edging
While performing wire edging, the edge of the sheet metal is rolled over on a metal wire, giving the sheet strong edges.
It is an old but very helpful method of making the sheet metal piece stronger.
# 3. Grooved seaming
A seam is a joint where the two ends of the sheet connect with each other.
To attach them grooves are used, which gives the required structural strength to the sheet metal.
# 4. Changing the profile of the sheet
The profile of sheet metal is an important thing that can provide strength to it if changed.
Changing the profile could be done by giving a bulge or a curve to the sheet metal simply by a hand tool like a hammer and a sandbag or a die press.
What are the tolerances on sheet metal parts?
Tolerances refer to deviations from perfect accuracy when manufacturing sheet metal parts.
Even though the vast majority of modern machines produce pieces with extreme accuracy, it doesn’t mean that the deviations will be 100% avoided.
So, during the creation of the blueprint, it is very important to consider such deviations and include tolerances in the formula.
It’s important to know that tolerance requirements and allowances differ from one manufacturer to another.
As an example, you can view the الصفحة التالية.
What is the difference between coated and non-coated parts in sheet metal?
The differences are the following:
- Coated parts have an inert surface most of the time.
- Coated parts have a higher resistance to wear.
- In the better part of cases, coated parts are harder than uncoated, especially if the hard coating was used.
- Coated parts do not react with the surrounding environment and get oxidized.
- Coated parts have higher corrosion resistance.
- Coatings might be permanent(electroplating) or, temporary(paint). In any case, it gives protection from environmental corrosion.
Note: if the part is uncoated, it does not always mean that it is somewhat worse.
E.g. some metals already have high corrosion resistance properties, so you don’t have to coat them.
What kind of fasteners are used with sheet metal?
Fasteners that are commonly used on sheet metal include rivets and sheet metal screws.
How to inspect sheet metal parts?
It is very important to check the quality of sheet metal parts before they are sent to the buyer.
Sheet metal parts are often used in the most safety demanding areas such as aerospace or automotive industries.
Even if we are talking about less demanding areas, it is still important to implement standards for high quality.
There are lots of tools to inspect sheet metal pieces, including:
- Micrometer.
- Caliper.
- Protractor, etc.
Please, use the following link if you want to learn more about the sheet metal inspection.
How to stamp sheet metal parts?
Metal stamping is a cold-forming process that makes use of dies and stamping presses to transform sheet metal into different shapes.
Pieces of flat sheet metal typically referred to as blanks, is fed into a sheet metal stamping press that uses a tool and dies surface to form the metal into a new shape.
What is the K factor in sheet metal? What is the difference between the K factor and Y factor?
The K-factor is the correlation of the neutral axis to the thickness of the sheet.
The K-factor is used to calculate flat patterns because it is related to how much material is stretched during bending.
The value of the K-factor should range between 0-0,5.
This value can be calculated taking the average of several samples and making the measurements of bend allowance, bend angle, material thickness, and inner radius.
Afterward, use the formula from the picture below:
Similar to the K factor, the Y factor is a constant used to calculate the sheet metal part developed length.
Y-factor and K-factor are directly related to each other, as you can see the following formula:
Y-factor = K-factor * (Π/2)
What is a joggle in sheet metal?
Joggle process (also known as joggling) is one of the types of bending.
In such a case, you can form multiple bends on sheet metal at the same time.
Often, these bends are in opposite directions and less than 90°.
Can KDM sheet metal parts be used for cars and trucks?
Yes, there are a lot of ways to use sheet metal parts in the automotive industry.
The thing is that sheet metal parts have good resistance properties, as well as lightweight.
These features make them a great choice for all industries, where lightweights and robustness of pieces are needed for safety and effective functioning.
What is the HS code of sheet metal parts?
HS stands for the Harmonized System.
It is an internationally standardized system of names and numbers for various traded products that are placed into groups.
If you want to ship sheet metal parts from China, it is important to know this code.
You can view proposed HS codes for such items visiting the الصفحة التالية.
How to estimate costs when buying sheet metal parts?
There is no single practice of cost calculation for sheet metal due to significant differences in the manufacturing of various parts.
Please, contact the KDM support team to require estimates for your particular order.
Galvanized sheet metal parts: what are they?
Galvanization is the process of applying a layer of zinc over the sheet steel to protect the metal beneath it from corrosion and rust.
For replacement parts, the presence of galvanization dramatically improves corrosion resistance and the life expectancy of parts.
How long does it take to get an answer from you?
KDM is making all the efforts to save time and money.
Leave us a quote and we’ll get in touch within one working day.
Can I require a sample of sheet metal from KDM?
KDM would be glad to send you a sample within three working days.
The delivery time depends on your location.
How much time is needed for KDM to fulfill my sheet metal parts order?
KDM specialists can create the CAD drawing of the needed parts within one working day.
The time of development depends on the quantity of your order.